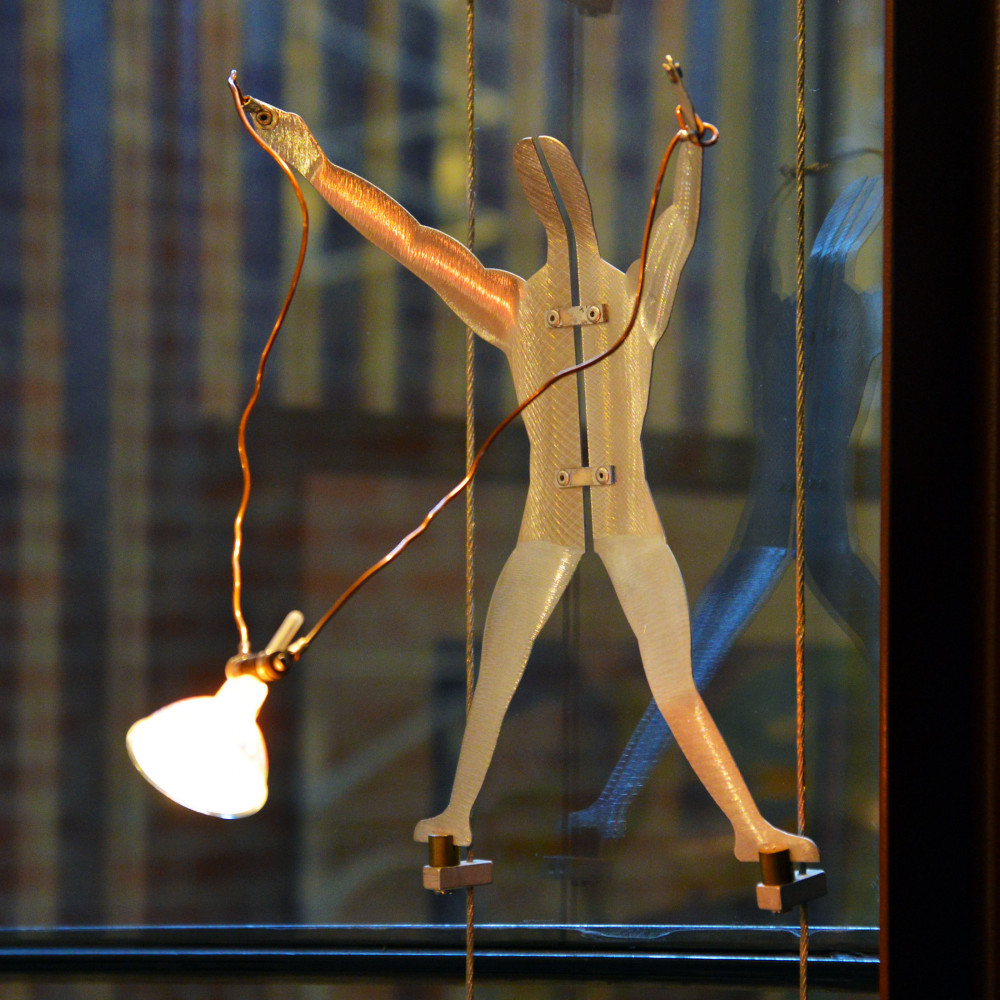
This article is somewhat technically oriented, but it is also about the larger picture. Our design focus favors taking forward-looking, intelligent advantage of emerging but proven technologies. What we are doing 'under the hood' enhances our work with improved economies and performance - weaving the technical with the artistic, the poetic with the practical, the dreams to the realities.
So even seemingly mundane and industry-bucking avenues for ways of doing things more intelligently are of of interest to us, and the topic we are discussing here is a prime example. It is hard not to notice that most of the electrical devices that surround us at home or at work operate on low voltage, DC (Direct Current) electricity. The construction industry continues to 'default' to wiring virtually everything in buildings to high voltage, AC (Alternating Current) electricity... which is less safe, less efficient, and ultimately more expensive, for many reasons we will get to shortly. Why is this? We think it's mostly about inertia, and resistance to change and innovation.
Low voltage power offers what can be an efficient and cost-effective alternative to traditional high voltage systems. Low voltage systems run on voltages lower than 30 volts DC (usually 12, 24, or 48 volts) and use a 'Class 2' power source. This is much safer during installation, maintenance, and use. Consequently, these systems carry different, far more lenient electric safety code requirements.
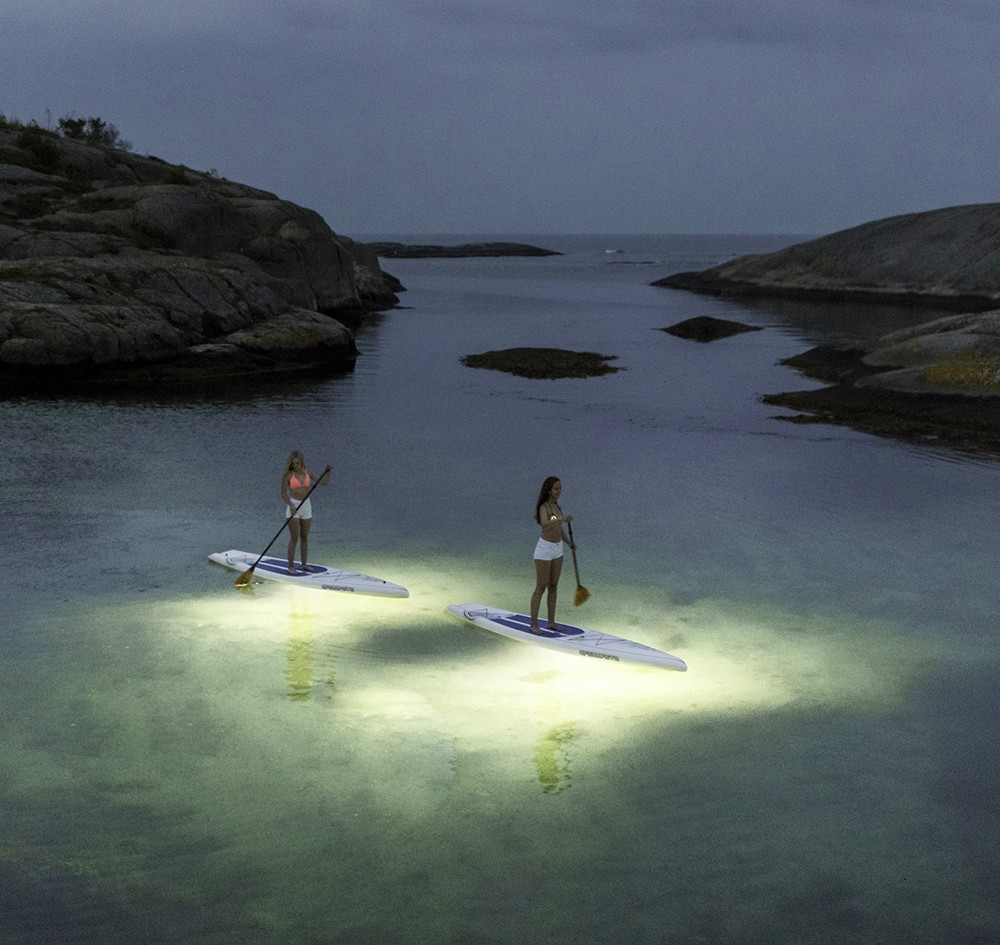
High voltage AC electrical systems are really great for things like transmission lines. Our power grid could not function without it. And there are many electrical devices, like pumps, that need high voltage to operate. But the vast majority of electrical devices in our homes or offices either can run on DC power, or already do. Think of boats, ships, airplanes, recreational vehicles, etc. which operate primarily using DC systems for everything electrical. There is really no reason we cannot use these systems in our buildings as well, and there are many good reasons to consider doing so. Everything about this possibility leads toward dramatically higher efficiency, lower cost, and higher safety. This is particularly true if we are working with on-site renewable energy sources (solar, hydro, wind), which, in contrast to power from the utility grid, is generally all low voltage DC power. Far better to simply use the electricity in that form than to go through the extravagant process of stepping the power up to high voltage with an expensive inverter, only to then have to convert it again back to DC at most points of use.
For most projects, some combination of high and low voltage electrical systems are already being installed. And for most projects, this will continue to be the case, but there is a dramatically increasing potential for the balance to shift far more heavily in favor of low voltage systems. Nowhere is this more true than with lighting.
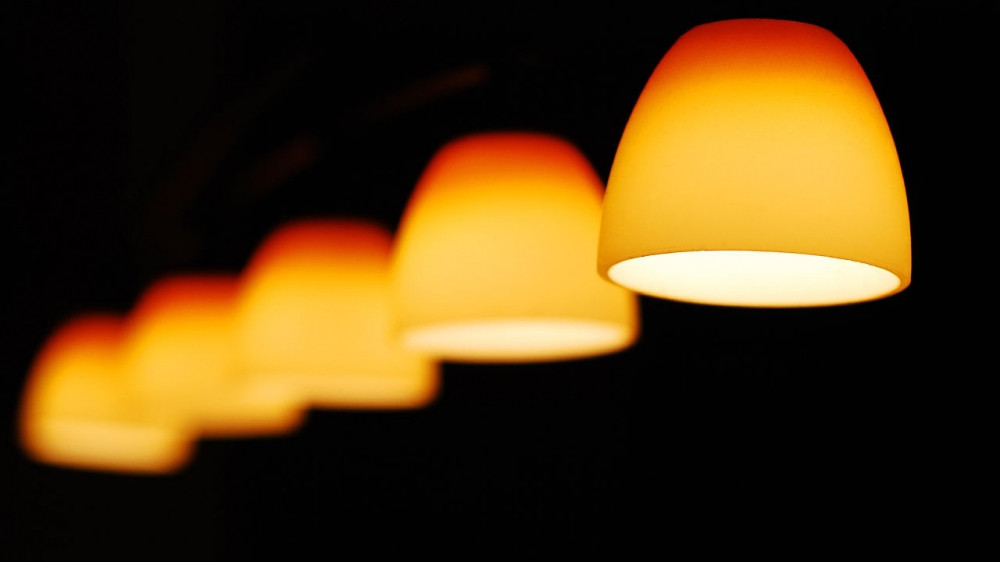
One of the largest electrical draws in buildings are the lighting systems. LED technology has improved in quality, reliability, and cost to the point where it is now the defacto choice for nearly all lighting in our projects. LED lights all run on low voltage power. Most of the cost of most LED light fixtures is tied to the fact that in anticipation of being wired to a high voltage electrical system, each fixture has a transformer integral with it to convert the power to low voltage. An alternative to this approach is to install one remote transformer that can power multiple lights. Using fewer transformers is an option that can reduce initial costs, operational costs, and future maintenance.
Low voltage lighting systems were originally developed in the 1950's but have mostly been used for landscape lighting and some recessed and cabinetry lighting. With the performance and pricing of LED lighting, it is now an option for far more lighting applications. The lower wattage of LED lamp fixtures provides improved performance for a mere fraction of the energy use of other lighting. They also run much cooler than other lamp types. There is reduced risk of combustion of the lamp itself, as well as a decreased chance of the fixture burning items placed near to it. LED dimmers can further reduce power consumption, and provide mood lighting. The dimmers must be compatible with the specific LED light. Color output from LED lighting is also variable. LED lights are also durable, with service lives measured in decades.
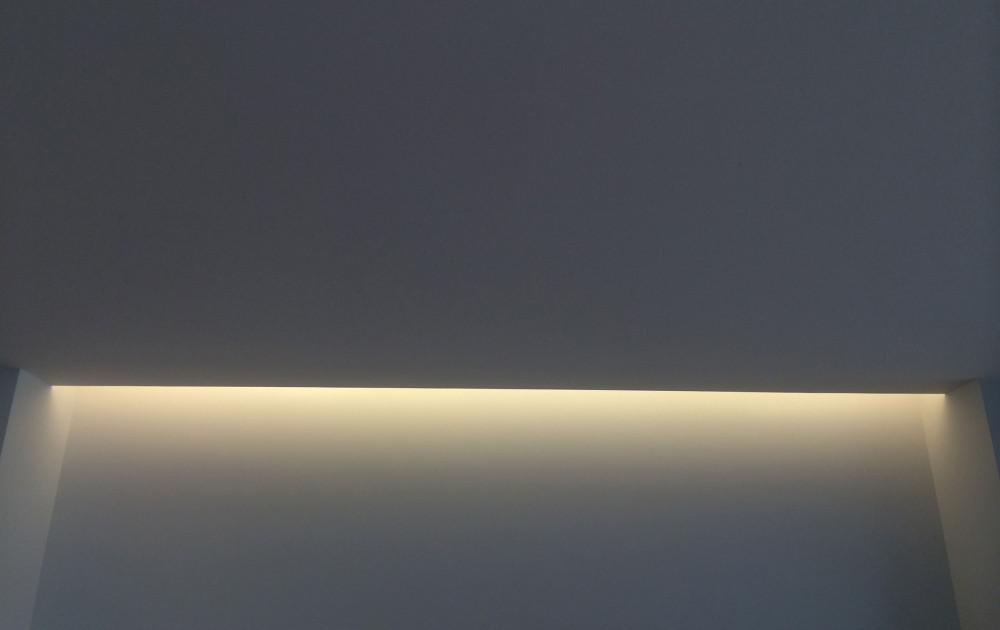
Track and cove lighting are often used for accent lighting. Cove lighting can provide soft light to a space, and track lighting can provide general lighting to a specific area or highlight artwork in a home or gallery. Kitchens, bathrooms, bedrooms, and hallways are just a few spaces that can benefit from low voltage lighting options. Because they can rely on remote power sources, LEDs powered with low voltage permit creative placement of lighting. Spaces where track or cove lighting is not an option with traditional lighting systems may now feature these types of lighting. For projects with space constraints, lighting fixtures that include the power source require ceiling or wall space to house the fixture, but a remote power source only requires that wires run through the space. This increased flexibility means we can totally rethink many lighting situations.
Another benefit of LED lights is that they typically produce far less heat than other forms of lighting. This saves energy by reducing the need for cooling. In areas where lights are installed adjacent to insulation, any light fixture must be rated specifically to allow that. When the driver for an LED light is built into the fixture, a thermostat will shut the fixture down if it reaches a threshold temperature, but if a remote driver is used, not only is installation simplified, but there are no concerns about proximity of the driver to insulation. Last but certainly not least, it is far easier to maintain airtight construction with the simplified installation requirements of light fixtures with remote drivers and low voltage wiring.
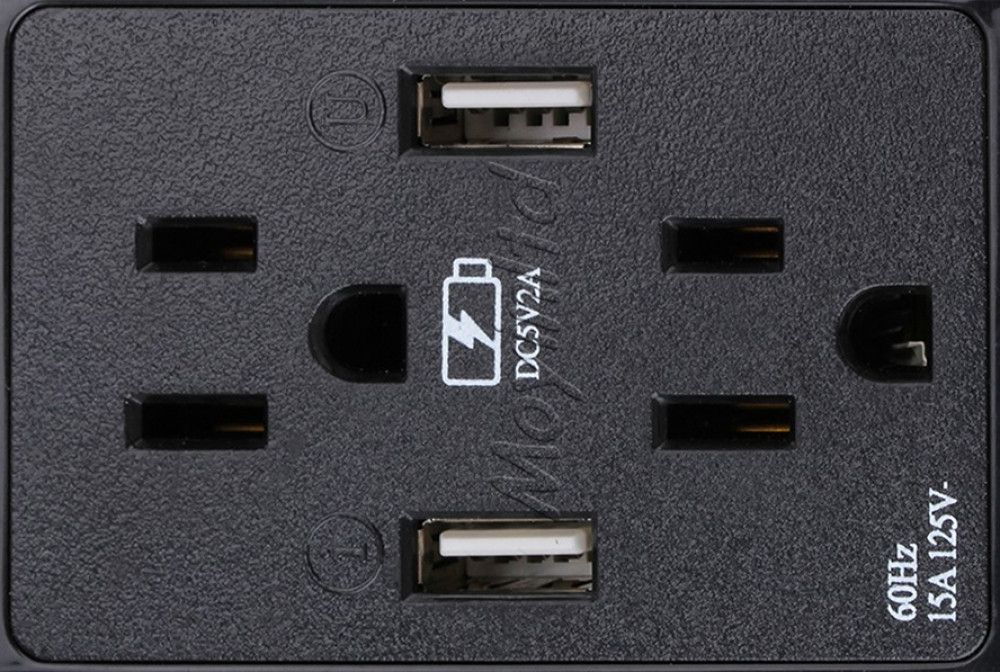
Unlike high voltage, Class 1 wiring, Class 2 wiring need not be installed by a licensed electrician. High voltage power may be run to a central driver location ideally, within 50 feet of wire length from lighting, depending on the system and wire types), and then all wiring downstream of the drivers may be Class 2. Class 2 wiring does not need to be inside a conduit or junction box, nor does it need to be grounded. Any skilled installer can work with Class 2 wiring. This flexibility can help with both electrical installation schedules and budgets. Working on low voltage power is safer because of the greatly reduced risk for shock and reduced use of conduit and junction boxes. Maintenance can be performed by skilled installers rather than licensed electricians, whereas for traditional lighting systems a trained electrician is the safe choice.
Compared to traditional electrical systems, low voltage power is easier, more efficient, and less disruptive to building occupants to service. Consolidated into central locations, remote drivers can be located in places where they are easier to access and maintain. Maintenance is generally easier because there are fewer of them, and they can be located in spaces which can make scheduling of maintenance easier as well. So for example, in a hotel or hospital, repairs can occur without having to disrupt the guest or patient.
Because LEDs run on low power, back-up batteries for lighting systems can generate light for a longer time than a traditional system, or can provide more light from a smaller battery. Low voltage power systems with LED lighting can benefit from having emergency backup drivers. If a property uses low voltage LEDs for general lighting, the fixtures can easily connect to a battery-powered backup driver which can provide sufficient power for several house. This is also true in the case of emergency lighting to illuminate the path of egress in commercial and public spaces, as set by the Life Safety Code, the National Electric Code, and the International Building Code. These institutions define the illumination required for emergency situations. With their low wattage and longevity, LED fixtures can work well to supply emergency lighting. They can run on supplementary power sources such as an integral auxiliary battery pack or remote mounted unit inverter. Battery packs as backup drivers work well because they can be easily placed wherever illumination is needed rather than being mounted on a wall. Unit inverter equipment can be installed remotely in places such as utility rooms, and can deliver AC power to LED drivers during a power loss. The power is relayed through a dedicated circuit from the inverter's battery supply.
Low voltage systems that use LEDs for general lighting can rely on integral emergency battery packs for emergency power These are UL Component Recognized in the U.S. and Canada, and thus are compatible with LED lighting systems. Lighting fixtures that have these battery packs installed will be certified as complying with UL 924 requirements. Emergency lighting is usually set up to work for about 90 minutes. These remote drivers can provide constant voltage, constant current, or constant power, depending on the system. Constant voltage will power LED arrays with a steady voltage regardless of current. While the light may be reduced as the batteries draw energy, they will illuminate 'up to code' for the required duration. Constant current battery packs provide a steady output of current, regardless of changes in voltage. The performance of these packs is dictated in part by the voltage requirement of the LED lighting. Illumination will degrade as the battery drains. Constant power battery packs are considered to be superior over the other two types because the constant power ensures that the illumination level will remain steady over the course of the 90 minute emergency duration.